Deuce HiBoy Resurrected - 12-05 Done!
Oct 12, 2013 8:44:38 GMT -4
Post by BERNARD "HOT ROD" KRON on Oct 12, 2013 8:44:38 GMT -4
This is a project I first started 5 years ago, long before I joined this forum. It was just months after I had gotten back into modeling after literally decades away and I had just discovered the wonderful world of aftermarket resin parts; more specifically the spectacular products produced by Norm Veber at Replicas & Miniatures Co. of Maryland. I was already on my second order from them and had obtained one of the Rik Hoving mastered traditional Deuce chassis with the buggy spring rear end. In fact almost half this car was made with RepMin parts!
Things started sort of bass ackwards for me since I usually do the motor and chassis before I do paint and body work, even now. Instead, in this instance I began painting immediately, using Duplicolor Aquamarine Blue metallic. The chassis I used was the Replicas & Miniatures of Maryland traditional ’32 Ford chassis by Rik Hoving which uses the Revell ’29 Ford suspension bits. With a full hood with the standard louvers, p/e grill and post ’49 Flatty with three carb setup, it was to be a classic early 50’s street rod. Details included RepMin stock ’32 firewall, p/e Auburn dash from RepMin, and the nice tuck and roll interior from RepMin that Lyle Willits mastered. All these parts are still available today and are, as always with Norm Veber’s products, absolutely the finest resin parts available.
I was striving for period authenticity which was partially the reason I bought so much RepMin stuff. There’s nothing out there better for that effect when building an old skool rod. Additional details included front suspension from the Revell ‘29/’30 “rat rod” Ford kits, finned Buick front brakes from RepMin, a quick change rear end, the flathead V8 from the (at that time recently released) Revell Deuce Tudor kit modified with a RepMin LaSalle transmission and highly detailed triple Stromberg 97’s from Model Car Garage, and a p/e grill shell. As you can tell I was aftermarket crazy at the time!
Here are some build picks from 5 years ago. As you can tell the stance is pretty lame. At the time I made excuses for it as being “period correct” but the truth was that the more work was required than I knew how to do back then. My excuse was even lamer than the stance!
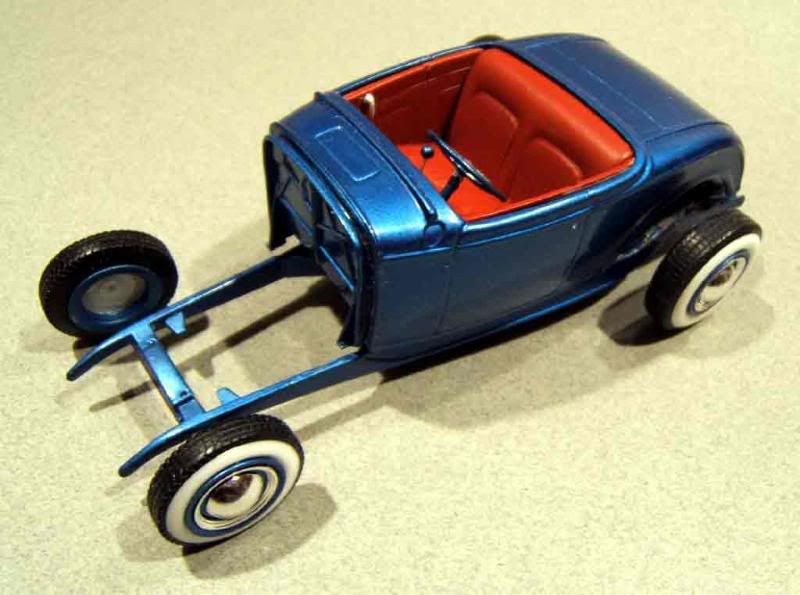
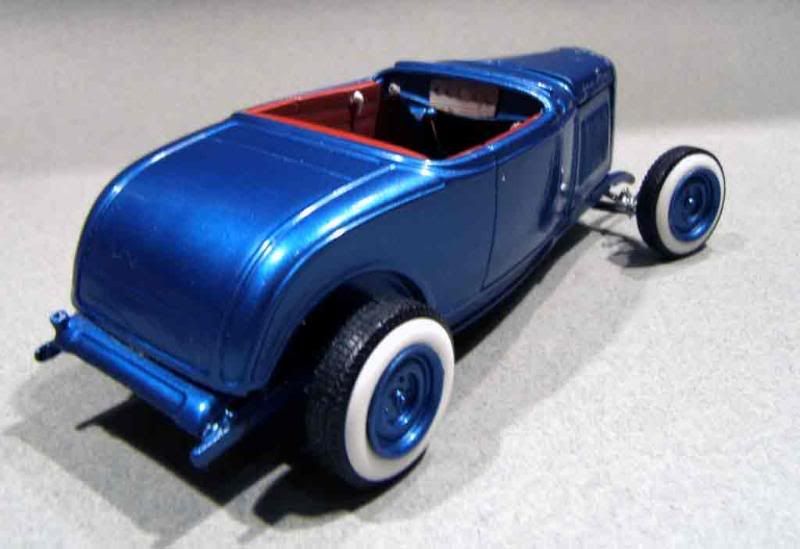
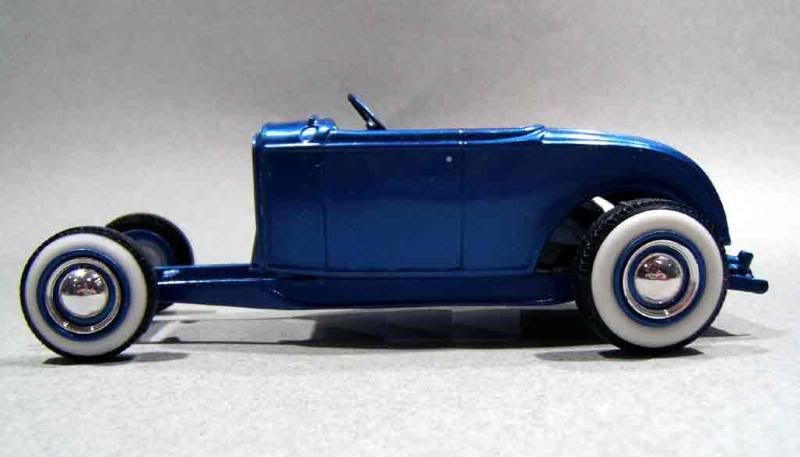
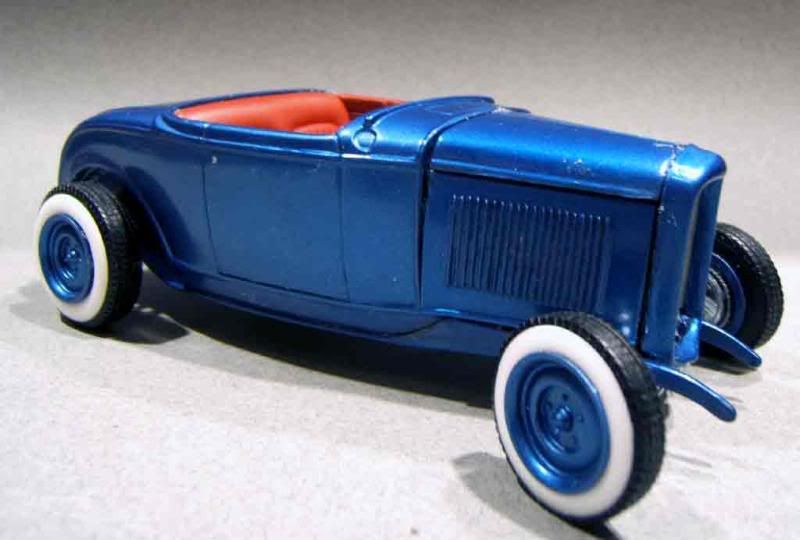
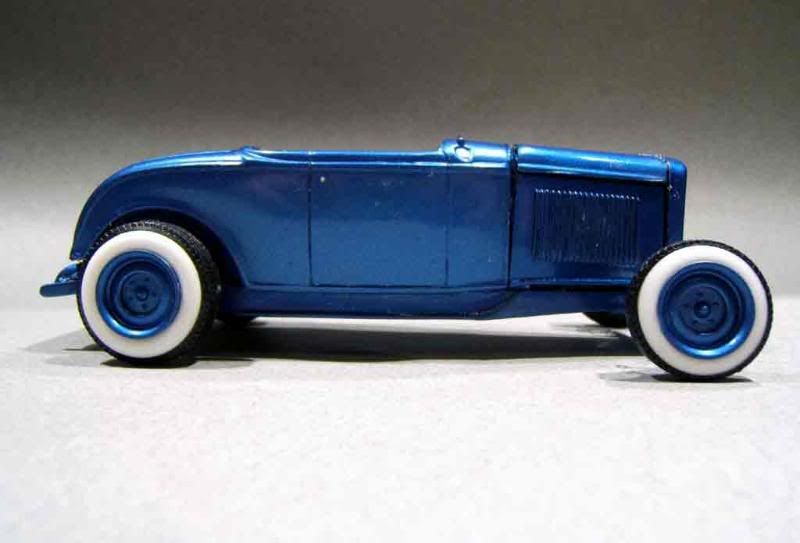
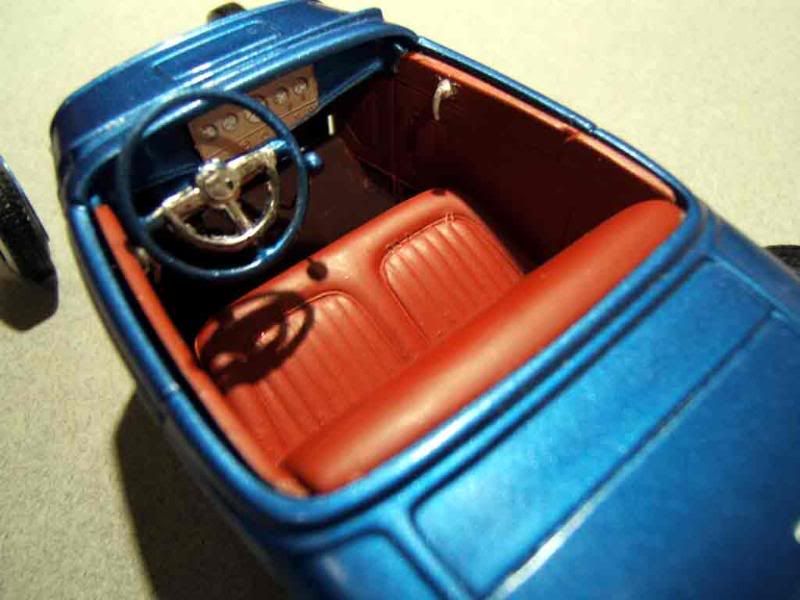
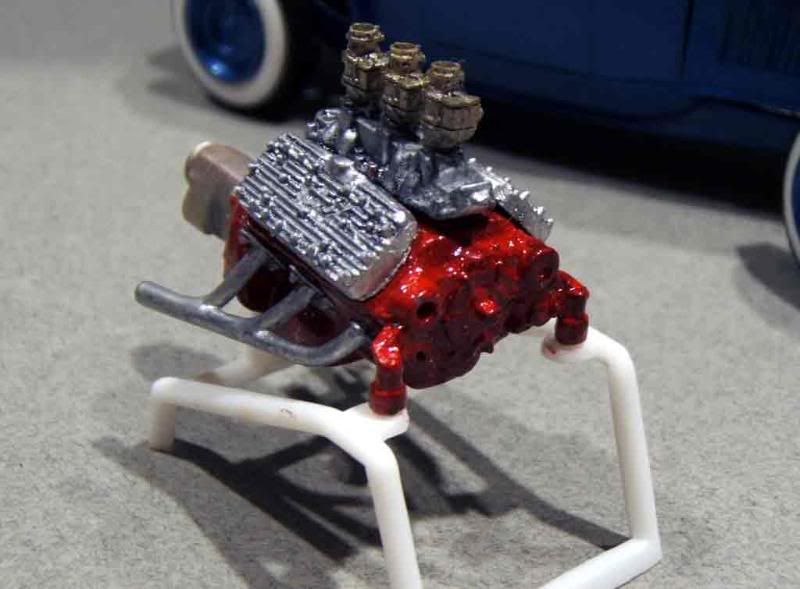
Well this one turned out to be my first DNF after my return. I was in way over my head. Norm Veber’s resin is famously thin, smooth and styrene like, but one result of his delicately fine castings is that they don’t take to heat real well. Soon I had warped parts on my hands from using my newly acquired dehydrator and the whole deal was quickly becoming the Project From Hell. For the first time (but far from the last) I put all the parts away in a box and moved on to happier days.
I never forgot the car. Every year or so I would open the box and think about how to save it. It had a great color, the RepMin resin interior based on the Monogram ’32 Ford Roadster looked fine, and Norm’s hot rod big ‘n’ little whitewalls had the perfect vibe. Sure, I never got the stance right and the resin chassis was dangerously thin and delicate. The posable front suspension from the Revell ‘29/30 “rat rod” Fords had given me no small amount of grief, too. But time has moved on and thankfully my skills have improved from those early days. The time has come to tackle this sucker and finish it up.
So I opened the box once more the other day and much to my horror discovered that the right chassis horn had snapped off, that the right kingpin was missing on the front axle and that the fuel tank underside was warped. This time however I think I’m up to the task. So I began by building up a new chassis from a Revell 1/25th Deuce, replicating as much as possible Hoving’s design in order to assure a proper fit. Miraculously, a can of paint appears to have survived so I can match it to the body. I also have addressed the stance issue, although the car isn’t yet back up on its wheels. The pictures and captions below will tell the tale…
The original Hoving chassis with its thin K-member and side rails. For some reason I never took a picture of the nicely done separate floor board that it comes with. It’s pictured below. I’ve made a mental note to ask Norm if he’ll sell me some separately from the chassis. They could come in mighty handy!

The results of 5 years of neglect and clumsy handling. This picture was taken after I had cut the rear cross member out to re-use on the new chassis.
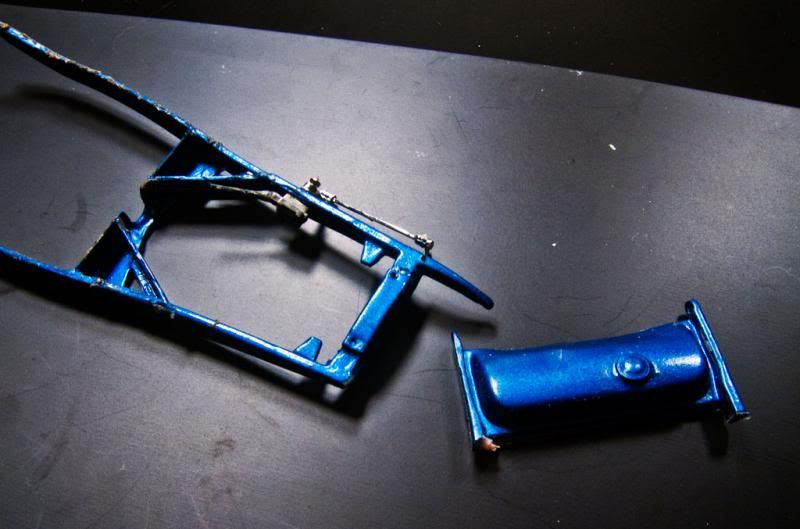
Topside view of the completed replacement chassis. The original fuel tank top is taped in place to check body fit. Anything white is genuine Revell styrene. The result is extraordinarily similar to Hoving’s design, but it’s far more robust and rigid than the thin resin original. I used the rear cross member from the RepMin piece to ensure proper fit of the existing rear axle and spring which survived intact. A Revell ‘29/’30 “rat rod” Ford rear cross member would work just as well. It’s probably what Hoving used on his master. The rear cross member is glued in place with epoxy. Just as Hoving did, I had to notch the bottom edge of the rail a bit to clear the rear axle. At the front Hoving flipped the Deuce cross member upside down and reshaped it to take the Revell front spring. For reasons of rigidity and strength I left the front cross member intact and modified it to lower the front end to help improve the stance.
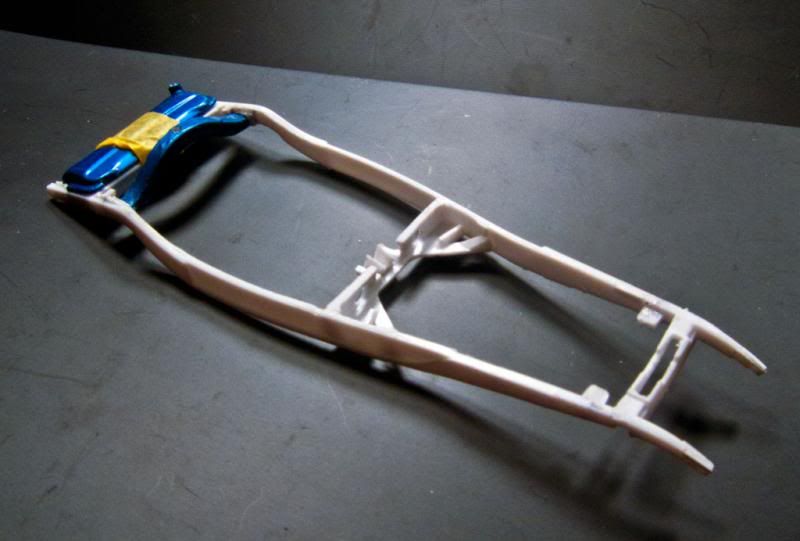
The underside of the front end. Note that I hogged out the inside of the cross member to allow the spring to sit more deeply into it. I also notched the rails to clear the spring ends. Finally, not shown here, I shaved three leaves off the top of the spring. All this puts the front axle center line just above the tops of the frame rails and lowers the front a good 2 scale inches or so. Also, note that like Hoving I moved the engine mounts forward, shortening them so they support the Flathead V8 I’ll be using.
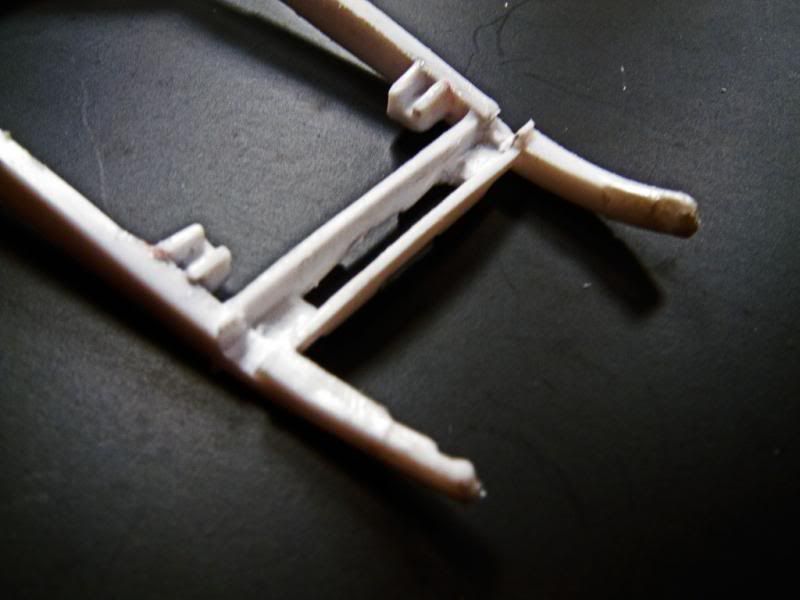
Bottom view of the frame showing the RepMin supplied floorboard assembly. The Revell chassis has the floorboards molded to it. I removed them and shaved the side bits of plastic all the way down to the tops of the chassis rails for a snug fit.
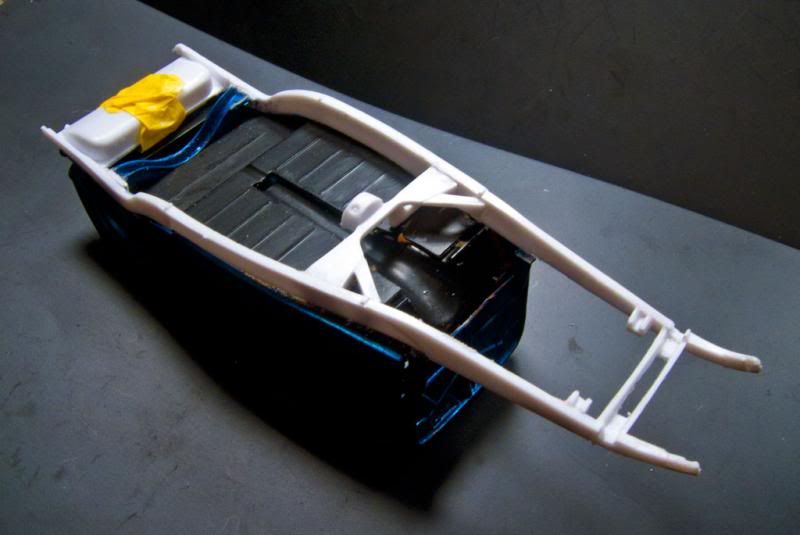
The separate floorboards without the chassis in place. It’s a single piece and includes an inset panel for the buggy spring. I had glued it in place at the time of original construction and it just won’t budge. Fortunately the funky contact cement residue seen in the picture is hidden by the chassis rails. I had just discovered I was badly allergic to CA and was just beginning to experiment with contact cement as a substitute. These days I use epoxy for all non-styrene joints almost exclusively. But there’s nothing like thin CA and a zip kicker for the tiny stuff. Ah well…
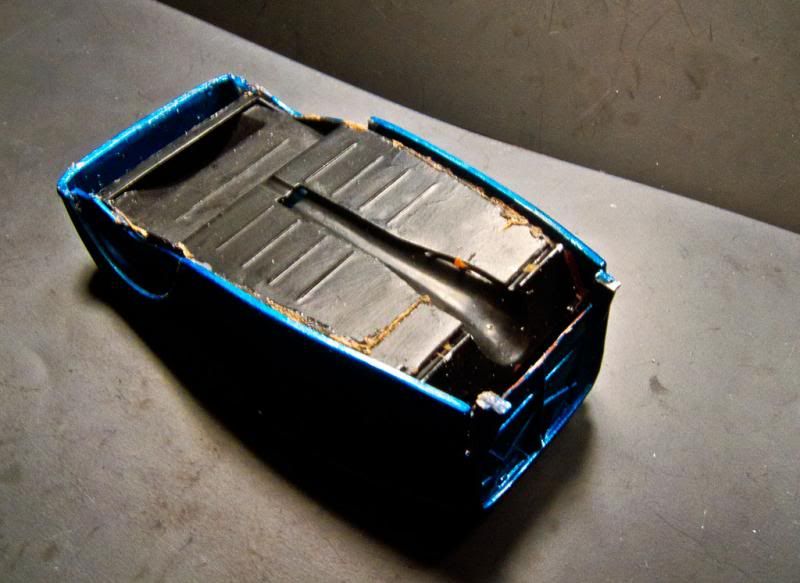
Next time… rescuing the motor and dialing in the fiddly suspension bits. Also, .will the paint match?
Thanks for lookin’,
B.
Things started sort of bass ackwards for me since I usually do the motor and chassis before I do paint and body work, even now. Instead, in this instance I began painting immediately, using Duplicolor Aquamarine Blue metallic. The chassis I used was the Replicas & Miniatures of Maryland traditional ’32 Ford chassis by Rik Hoving which uses the Revell ’29 Ford suspension bits. With a full hood with the standard louvers, p/e grill and post ’49 Flatty with three carb setup, it was to be a classic early 50’s street rod. Details included RepMin stock ’32 firewall, p/e Auburn dash from RepMin, and the nice tuck and roll interior from RepMin that Lyle Willits mastered. All these parts are still available today and are, as always with Norm Veber’s products, absolutely the finest resin parts available.
I was striving for period authenticity which was partially the reason I bought so much RepMin stuff. There’s nothing out there better for that effect when building an old skool rod. Additional details included front suspension from the Revell ‘29/’30 “rat rod” Ford kits, finned Buick front brakes from RepMin, a quick change rear end, the flathead V8 from the (at that time recently released) Revell Deuce Tudor kit modified with a RepMin LaSalle transmission and highly detailed triple Stromberg 97’s from Model Car Garage, and a p/e grill shell. As you can tell I was aftermarket crazy at the time!
Here are some build picks from 5 years ago. As you can tell the stance is pretty lame. At the time I made excuses for it as being “period correct” but the truth was that the more work was required than I knew how to do back then. My excuse was even lamer than the stance!
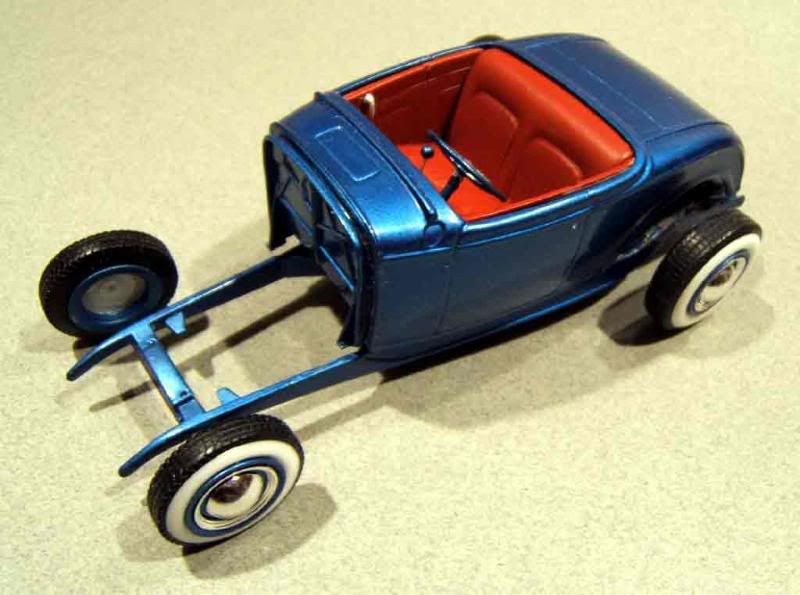
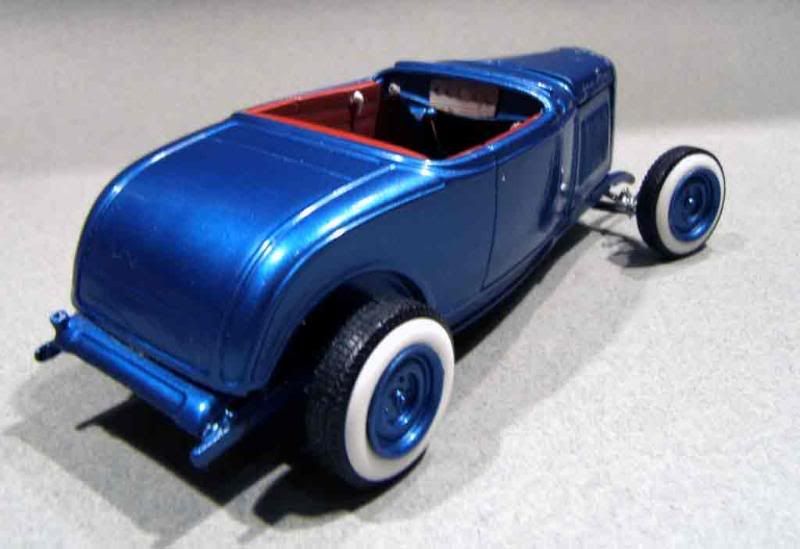
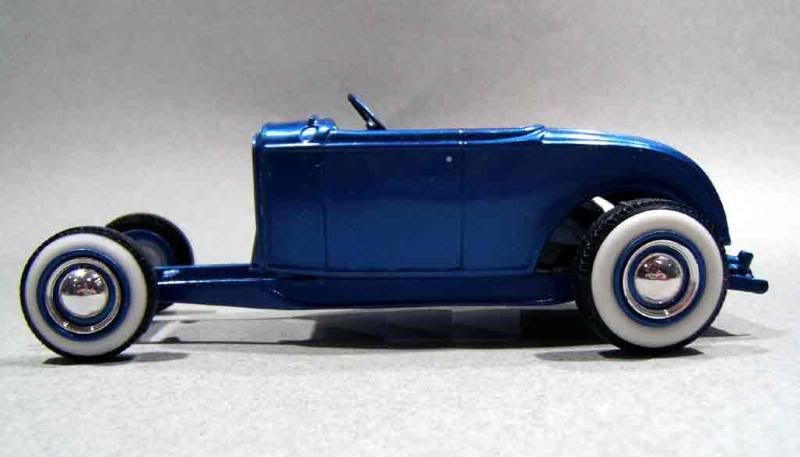
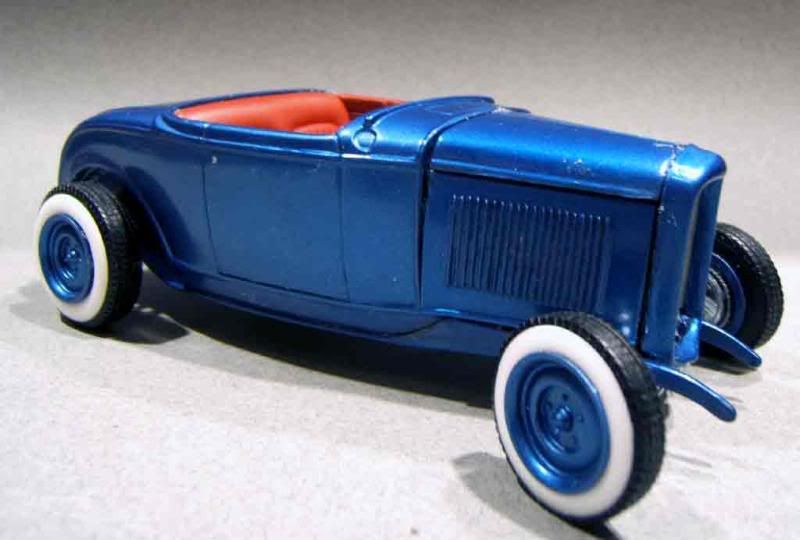
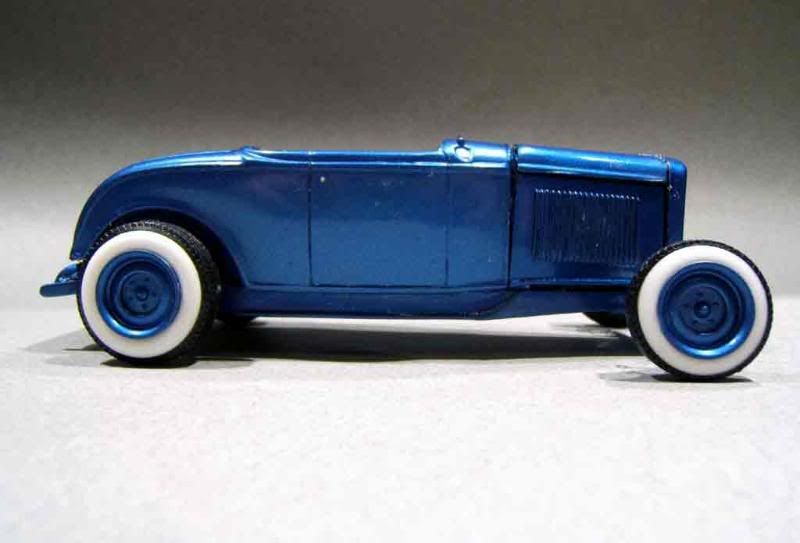
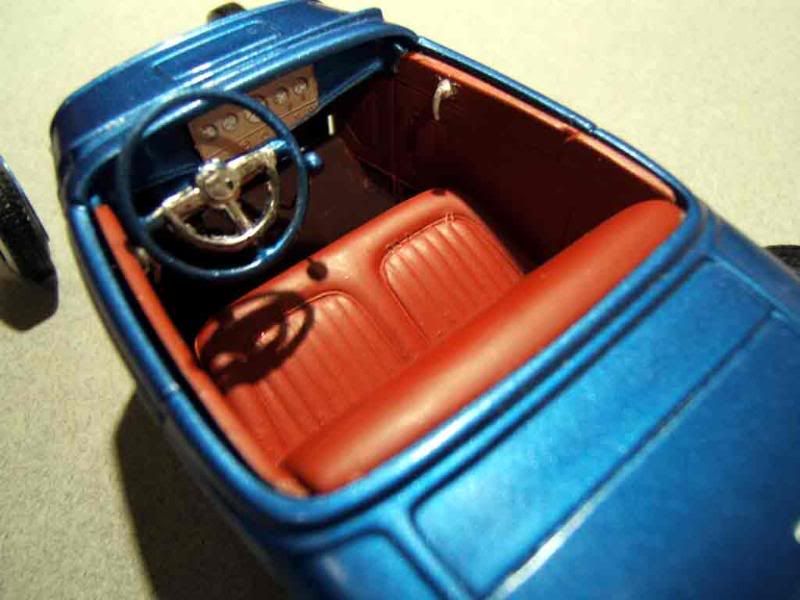
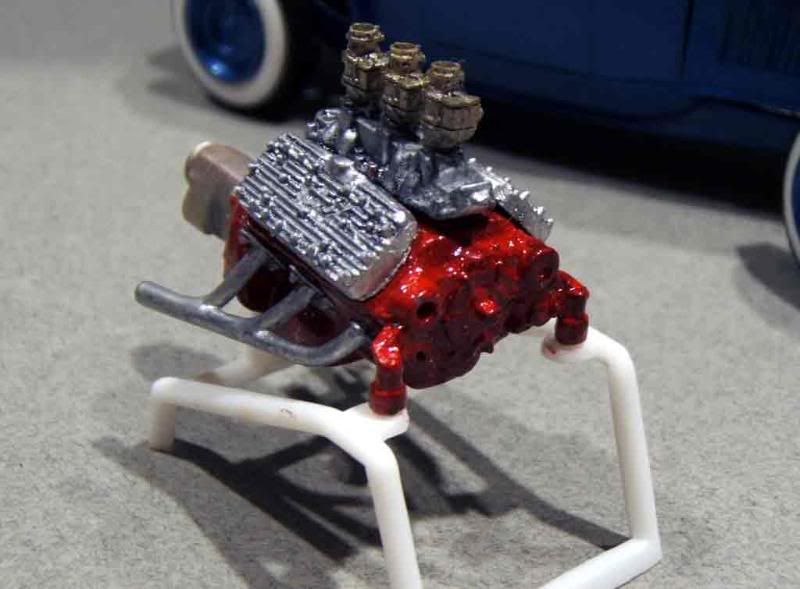
Well this one turned out to be my first DNF after my return. I was in way over my head. Norm Veber’s resin is famously thin, smooth and styrene like, but one result of his delicately fine castings is that they don’t take to heat real well. Soon I had warped parts on my hands from using my newly acquired dehydrator and the whole deal was quickly becoming the Project From Hell. For the first time (but far from the last) I put all the parts away in a box and moved on to happier days.
I never forgot the car. Every year or so I would open the box and think about how to save it. It had a great color, the RepMin resin interior based on the Monogram ’32 Ford Roadster looked fine, and Norm’s hot rod big ‘n’ little whitewalls had the perfect vibe. Sure, I never got the stance right and the resin chassis was dangerously thin and delicate. The posable front suspension from the Revell ‘29/30 “rat rod” Fords had given me no small amount of grief, too. But time has moved on and thankfully my skills have improved from those early days. The time has come to tackle this sucker and finish it up.
So I opened the box once more the other day and much to my horror discovered that the right chassis horn had snapped off, that the right kingpin was missing on the front axle and that the fuel tank underside was warped. This time however I think I’m up to the task. So I began by building up a new chassis from a Revell 1/25th Deuce, replicating as much as possible Hoving’s design in order to assure a proper fit. Miraculously, a can of paint appears to have survived so I can match it to the body. I also have addressed the stance issue, although the car isn’t yet back up on its wheels. The pictures and captions below will tell the tale…
The original Hoving chassis with its thin K-member and side rails. For some reason I never took a picture of the nicely done separate floor board that it comes with. It’s pictured below. I’ve made a mental note to ask Norm if he’ll sell me some separately from the chassis. They could come in mighty handy!

The results of 5 years of neglect and clumsy handling. This picture was taken after I had cut the rear cross member out to re-use on the new chassis.
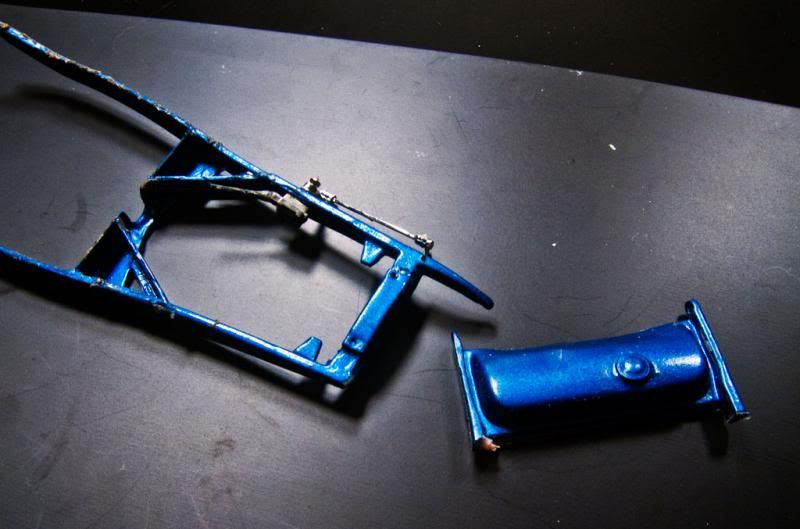
Topside view of the completed replacement chassis. The original fuel tank top is taped in place to check body fit. Anything white is genuine Revell styrene. The result is extraordinarily similar to Hoving’s design, but it’s far more robust and rigid than the thin resin original. I used the rear cross member from the RepMin piece to ensure proper fit of the existing rear axle and spring which survived intact. A Revell ‘29/’30 “rat rod” Ford rear cross member would work just as well. It’s probably what Hoving used on his master. The rear cross member is glued in place with epoxy. Just as Hoving did, I had to notch the bottom edge of the rail a bit to clear the rear axle. At the front Hoving flipped the Deuce cross member upside down and reshaped it to take the Revell front spring. For reasons of rigidity and strength I left the front cross member intact and modified it to lower the front end to help improve the stance.
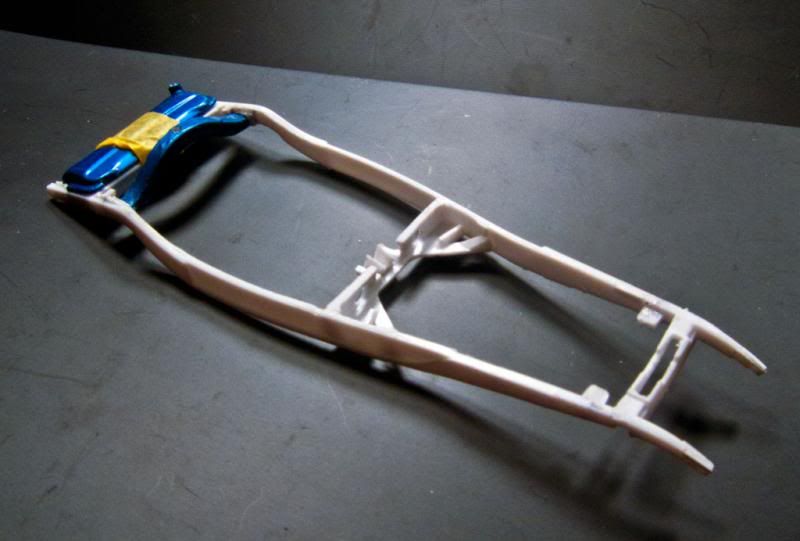
The underside of the front end. Note that I hogged out the inside of the cross member to allow the spring to sit more deeply into it. I also notched the rails to clear the spring ends. Finally, not shown here, I shaved three leaves off the top of the spring. All this puts the front axle center line just above the tops of the frame rails and lowers the front a good 2 scale inches or so. Also, note that like Hoving I moved the engine mounts forward, shortening them so they support the Flathead V8 I’ll be using.
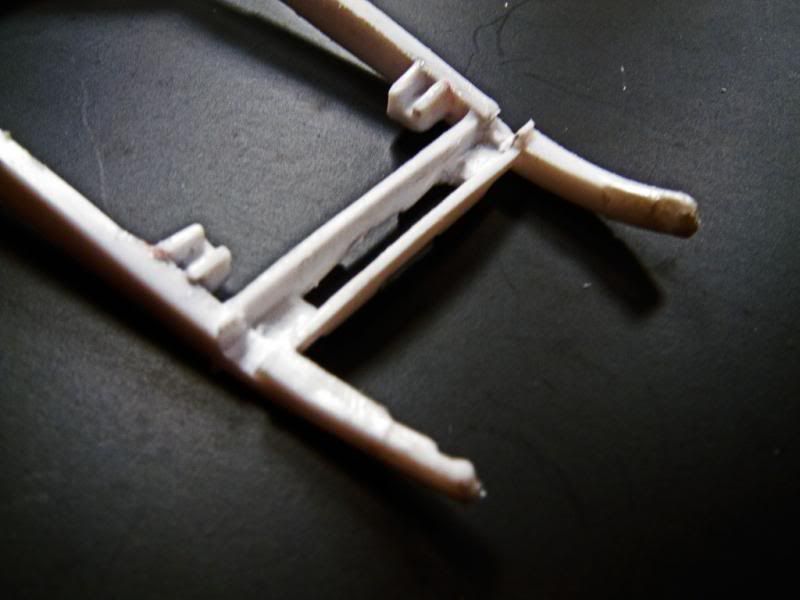
Bottom view of the frame showing the RepMin supplied floorboard assembly. The Revell chassis has the floorboards molded to it. I removed them and shaved the side bits of plastic all the way down to the tops of the chassis rails for a snug fit.
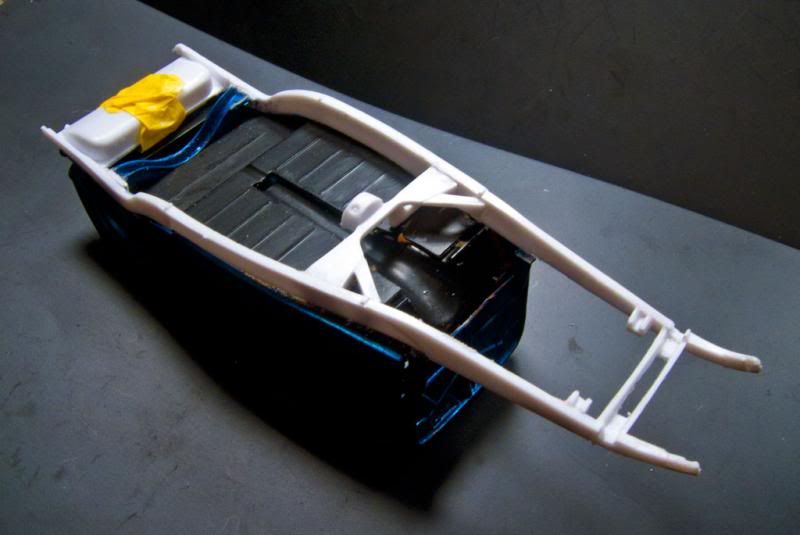
The separate floorboards without the chassis in place. It’s a single piece and includes an inset panel for the buggy spring. I had glued it in place at the time of original construction and it just won’t budge. Fortunately the funky contact cement residue seen in the picture is hidden by the chassis rails. I had just discovered I was badly allergic to CA and was just beginning to experiment with contact cement as a substitute. These days I use epoxy for all non-styrene joints almost exclusively. But there’s nothing like thin CA and a zip kicker for the tiny stuff. Ah well…
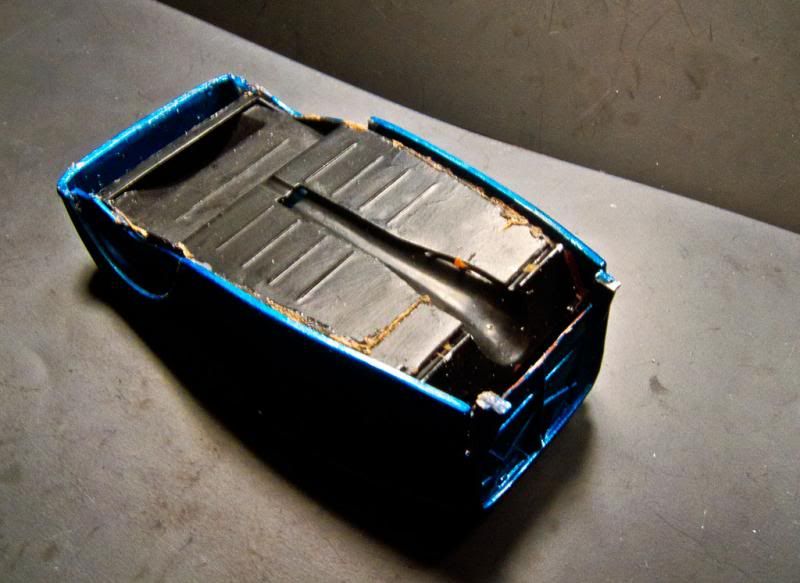
Next time… rescuing the motor and dialing in the fiddly suspension bits. Also, .will the paint match?
Thanks for lookin’,
B.